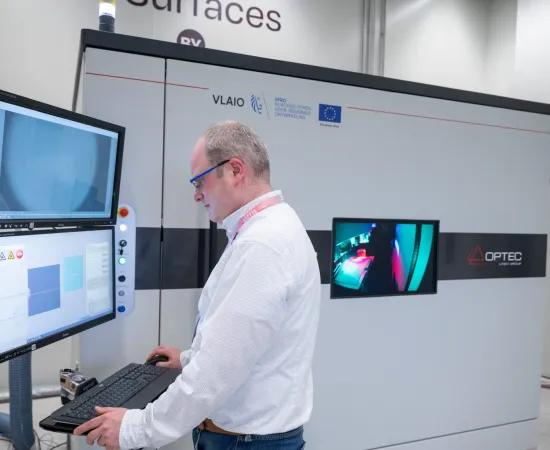
FEMTOFUNC | Biomimetic surface functionality by femtosecond laser texturing
Realising components with biomimetic surface functionality using femtosecond laser texturing
Femtosecond laser texturing represents a new opportunity to achieve biomimetic functionality by applying micro- and nanotextures to the surface of a component with particularly high finish quality. To promote this technology, which is considered environmentally friendly on several levels, industries and educational institutions must be sensitised and inspired to incorporate laser-textured functionality into their scope.
Context
Throughout the last decade, Sirris has built up knowledge and demonstrated the feasibility of laser-texture materials surfaces to create various functionalities on two-dimension flat surfaces, resulting in several successful proofs of concept. However, to achieve a breakthrough in the manufacturing industry, applied research into 3D components becomes necessary. Figure 1 presents some examples of these functionalities.
- At the same time, it is important to raise the knowledge of laser surface functionalisation approaching different audiences, as for example industry professionals, students and general community. This initiative could foster future developments for new products, production process and skilled manpower in the Belgian manufacturing cluster.
Laser technology is considered environmentally friendly on several levels:
Product level: laser texturing does not add any material, ensuring reusability without the need for chemical cleaning processes. - Process level: laser texturing occurs without the consumption of supporting (chemical) resources and does not generate waste.
- Energy consumption: compared to current (electro / chemical) processes and treatments, laser texturing consumes only a minimal amount of energy.
Objectives
The project aims to realise three demonstrators to evidence the potential of laser-applied biomimetic textures in the context of circular economy, which are:
Anti-icing: assembling of a turbine blade (or alternatively, an airplane wing), an air foil shaped component, to be tested against ice build-up. The demand for improved anti-icing surfaces is of critical significance, and linked to several important aspects of our daily lives. Surface icing poses a threat, not only to the manufacturing sector, but also to human safety.
Anti-bacterial: testing a door knob component to determine whether the adhesion of bacteria will be reduced, or if the formed biofilm will be easier to remove compared to an untextured component. Avoiding the use of biocides and cleaning agents by using anti-bacterial texturing can have a significant impact in the food and pharmaceutical sectors.
Friction reduction: selecting a bicycle wheel bearing as a component to simulate the friction reduction property of laser texturing. Friction is an issue of enormous importance in mechanical engineering, and the use of lubricants and coatings is not only an additional cost but also an environmental burden.
Approach
The three components will be used to assess whether the laser-textured functionality is equivalent or better than the classical alternatives, and will be developed using the methodology proposed in Figure 2:
Additionally, the project aims to promote laser texturing technology through inspirational sessions and awareness-raising events in industries and educational environments. To do so, collective workshops will be promoted and will include presentations and live exhibition of the practical demonstrators. Participants will receive a small publication for reference.
Moreover, a number of companies will be approached individually for inspirational discussions to identify opportunities in their product range or production process. These discussions will involve various roles within the company, including design engineers, sales, production, etc., to consider different perspectives.
A promotional campaign will be conducted through the creation of supporting material, such as banners, posters, blog contents, and the publication of a “casebook” providing a comprehensive explanation of the potential of this technology.
To accomplish the full objective of this project, the applied methodology can be summarised as shown in Figure 3. This methodology was created to inspire and guide industries to adopt new technologies and creates concrete, tangible demonstrators to engage students and the general public.
Funding
BBBC – Belgium Builds Back Circular
Project Name:
- Realizing components with biomimetic surface functionality using femtosecond laser texturing
- Number / ID: I515043/BE-C[C53]-I[I-515]
More information about our expertise
Articles related to the FEMTOFUNC project
Ultrashort pulse lasers for surface functionalisation >
High-throughput femtosecond laser texturing of soft biopolymer coatings >
Laser manufacturing - enabling a circular and energy-efficient future >
Advancements in surface engineering: superhydrophobic surfaces and femtosecond laser texturing >