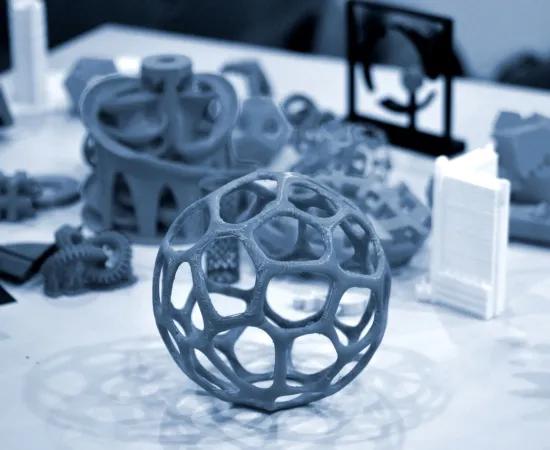
INSIDE Metal Additive Manufacturing
Flanders is one of the frontrunners in the field of Metal Additive 3D printing, but in order to achieve a large-scale breakthrough and lead companies to an industry of the future in Flanders (Industry 4.0), a number of barriers still need to be removed around material suitability and availability, insufficient and inconsistent material and product properties and production speed.
Context
Flanders is one of the frontrunners in the field of Metal Additive 3D printing, but in order to achieve a large-scale breakthrough and lead companies to an industry of the future in Flanders (Industry 4.0), a number of barriers still need to be removed around material suitability and availability, insufficient and inconsistent material and product properties and production speed.
The focus of the project was on the material side of additive printing with (high strength) steel and stainless steel. Powder bed (SLM), laser metal deposition (LMD) and Wire Arc Additive Manufacturing (WAAM) will be treated in the project. Throughout the entire project the link was made to existing knowledge and the comparison with conventional production technologies for the input materials, the process, as well as the properties of the end component.
Objectives
Allowing companies to make a faster and successful transition to the new production technology:
- Raising awareness of and information about the impact of material selection, process parameters, (thermal) post-treatment on the (micro-) structure and properties.
- Define guidelines for producing 3D printed pieces from ferro-alloys with good and consistent mechanical properties.
- Guidelines on certification and quality criteria for raw materials, processes and end products;
- Evaluate performance and cost of the 3D printed piece compared to conventional production techniques.
- Draw up a flowchart for the companies to identify the (im)possibilities of AM for their application and to orient them in their choice of material, process and aftertreatment for the production and use of parts with good and consistent properties.
Target group
The project is aimed at a broad target group of companies already active or with potential future activities along the entire value chain of 3D metal printing with (high strength) steels and stainless steel: (potential) producers of components via 3D printing, (potential) users, manufacturers of printing machines, aftertreaters (thermal treatment, surface treatment), suppliers of metals (powder, wire). The number of companies within this target group in Flanders is estimated at 240, of which the vast majority (92%) are SMEs.
Results
One of the objectives of the INSIDE Metal AM project was to make practical knowledge about steel printing accessible to the general public.
The use of the project results gives companies:
- Increased competitiveness through the supply/use of products with a higher added value ('customised', small series, longer lifetime, shorter delivery time, qualified) and lower production costs thanks to more consistent properties and efficient material deployment.
- Shorter learning curves for companies taking their first steps.
- Increased turnover for companies that print and supply goods and services.
The publications and presentations below contain an overview of the results obtained in the project, and includes relevant information for both people taking their first steps in 3D printing as well as people seeking for more expert knowledge on additive manufacturing.
White paper
- INSIDE Metal AM – 3D printing with steel: This white paper provides a summary of the lessons learned in the project, based on answers given to a number of specific questions. The topic covered include (1) raw material selection and quality; (2) printing and heat treatment of L-PBF steel, LMD steel and WAAM steel; (3) surface post-processing and (4) demonstrator parts.
Project reports
- Supply and selection of print materials (Project report, Dutch only): This project report discusses how to make an informed choice of materials. It also explains the main characteristics of metal powders that should be taken into account when ordering powder. The most common types of steel for 3D printing are discussed, supplemented by a list of suppliers. Finally, brief attention is given to the cost price and the possibility of having metal powders made to measure. The use of welding wire for WAAM technology is briefly explained.
- L-PBF and heat treatment of 17-4PH steel: This project report presents all the results from L-PBF printing with 17-4PH, starting from process optimization over heat treatment to printing of a demonstrator part. The most important lessons learned are conveniently summarized.
- Wire selection for WAAM – Quality insights (Complementary information): An overview is given of available WAAM wires, together with quality considerations.
- Quality of powders for AM (Complementary information): A brief overview is given of why the quality of powders is important, what the key characteristics are and how an efficient two-step testing procedure can be used to keep track of powder quality in your production flow.
- AM of aluminium extrusion moulds using H11 steel (Complementary information): This document gives information on the use of H11 steel for printing of aluminium extrusion moulds. It also presents a nice story of how starting small can lead to innovation, even if the value of 3D printing was not clear from the start.
- L-PBF vs. LMD - Case study using a generalised rotor (Complementary information): A comparison is made between the use of L-PBF and LMD for printing of a rotor designed within the project. An effort to make a cost comparison is also made, as well as a brief comparison to conventional manufacturing.
- LMD processing and testing (Complementary information) Additional insight of the results of LMD processing and testing of 316L and 17-4PH. It also contains information on the 3D printing of the generalized rotor demonstrator.
- WAAM processing and testing (Complementary information): This document tackles the parametrization of 3 welding wires: 316L, S355 and duplex steel, with a more detailed study of the later. It also discusses the processing conditions and limitations to print a large pump core demonstrator.
- Surface finishing of L-PBF and LMD parts (Complementary information): Surface finishing is applied on LMD and L-PBF parts. The results largely depend on the initial surface state and the combination of techniques: sandblasting, tribofinishing and electropolishing. It is thus important to have a good knowledge of the working principles and effect on the roughness to select the right combination.
Webinars
- INSIDE Metal AM project – 3D Printing with Steel, 27/10/2020
- INSIDE Metal AM project – Final Event, 22/02/2021
Presentations en publications
- Potential and challenges regarding additive manufacturing of steel alloys - The INSIDE project, Flam3D Info evening, 15/10/2019, Location: Aqtor!
- Laser Metal Deposition under the microscope - Basics, Applications and Challenges, Metallerie No. 2004, 14/05/2020. The publication list referred to in the article can be found here.
- Selection of print materials and available steel grades - 3D printing with metallic powders, Metallerie No. 2005, 30/06/2020