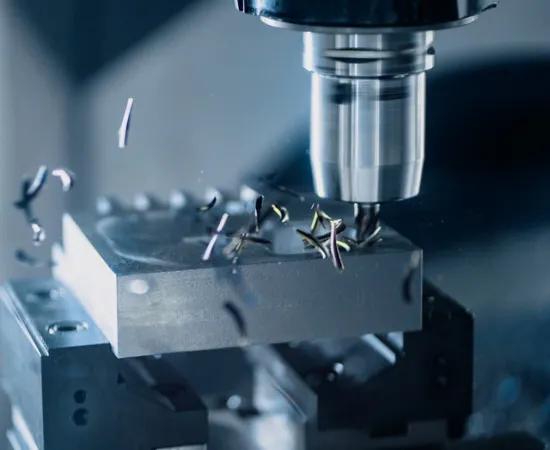
Model-based machining
Adaptive machining allows specific actions to be taken in machining, based on the actual production situation. The successful application depends on the availability of correct (real-time) data and the corresponding structured and digitalised working methods. For the latter, we have developed several models which we are now converting into practical tools and offer to companies within the 'Model-based processing' project.
Context
The manufacturing industry is facing major challenges in several areas, including making flexible changes to meet customer demands, increasing productivity, finding the right talent and making the best use of production technology. To find answers to these challenges, people are checking out the 'Industry 4.0’ concepts: a far-reaching digitalisation of production, in which (production) data is used to (autonomously) compensate for variations, integrate process knowledge, guarantee quality, etc.
Objective
The machining industry often uses the term of adaptive machining, i.e. taking specific actions based on the actual production situation. The successful application depends on the availability of correct (real-time) data and the corresponding structured and digitalised working methods. The first aspect is increasingly within reach thanks to the ever-growing range of hardware and software. For the second aspect, we must move towards 'model-based machining', where parameterised models (formulas) are used to identify the optimal machining process.
Within the project 'Model Based Machining', such (academic) models are further developed and converted into practical tools: online applications (apps) which run on data gathered on the shop floor, in order to make these machining models widely applicable and accessible. Specifically, applications are envisaged that provide support in determining cutting conditions. Each of the applications will be accompanied by a training package and demonstrations to facilitate transfer to and adoption in the workplace.
‘Optimal working zone’ model, for lower tool costs
The model structurally determines the optimum cutting zone(s) for a specific material. This includes a combination of cutting conditions, tools and cooling method... The model can be used, on the one hand, in case of premature or excessive tool wear, an acute problem that can mean the difference between profit or loss on an order, while on the other hand, also for optimising overall tool use.
‘Quick accuracy check’ model for a guaranteed final result
For a five-axis milling machine, a ‘quick accuracy check’ model and procedure are provided to ensure at regular intervals that the machine accuracy is good.
‘Stability curves’ model, for faster processing without vibrations
The vibration profile of a certain machine-tool-workpiece combination is mapped out by means of a low-threshold hammer test. This allows vibration-free machining conditions to be determined.
‘Cutting forces’ model, for optimal machining rate
For solid carbide tools, a heat map is generated that provides insight into the possible cutting conditions in a given material. The optimal cutting conditions for different operations (roughing, contouring, etc.) can thus be read.
‘Productivity’ model for a cost-efficient process
Ultimately, the individual elements or models together form a single machining process or operation , where productivity is determined by the combination of it all. The productivity model combines the results of the previous models, supplemented by financial data such , as depreciation and tool costs.
Approach
The various models can be consulted free of charge on an online platform. After a simple registration you will receive a link to the platform. You will find explanations on how to work with the models, but be sure to keep an eye on the Sirris agenda as well, as we will be organising both physical and online explanatory sessions.
The platform is still under construction, but register now and we will send you the link when it opens.
In addition, a user group is being set up. Members of this user group will not only be the first to gain access to the applications, but will also have the opportunity to give direction to the project. For example, as a member of the user group, you may suggest that the applications be developed initially for materials, tools and/or machines that apply to you. Participation in the user group is free of charge and only requires a limited investment in time by attending two meetings/year (physical or online) and of course giving feedback on the proposed applications (e.g. on their practical usability).
Target Group
The project is aimed at all companies with a machining activity. The platform is being developed as a practical tool suitable for use during work preparation, NC programming or quotation calculation as well as on the shop floor in the event of an acute problem or improvement.
Reference
VLAIO COOCK Modelbased processing, HBC.2021.0552